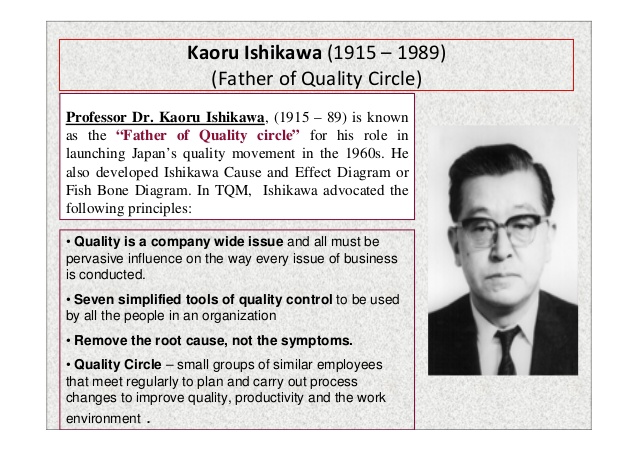
The life and death of Quality Circles
In the US, at least, “quality circles are almost universally consigned to the dustbin of management techniques.”
Why? What can we do to make a good idea even better?
In the US, at least, “quality circles are almost universally consigned to the dustbin of management techniques.”
Why? What can we do to make a good idea even better?